深度脱碳
氢能助力工业绿色转型
在双碳路上,越来越多的行业与“氢”同行。
国家工信部、科技部、自然资源部日前联合印发《“十四五”原材料工业发展规划》(以下简称《规划》)提出“组织研发富氢碳循环高炉、氢能窑炉、氢基直接还原等技术”,并要求实施氢冶金、非高炉炼铁等低碳冶炼试点项目,开展低碳水泥、氢能窑炉及固碳建材试点,明确了氢在工业减排中的作用。
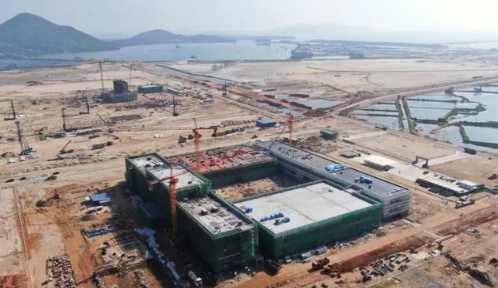
随着氢能产业发展热度持续升温,其在钢铁等工业领域脱碳中扮演的角色也逐渐得到认可。国家发展改革委价格成本调查中心近期发布的《钢铁产业供应链实现“双碳”目标路径分析及对成本的影响》也将“氢”摆到了重要位置。文章强调,钢铁绿色生产的工艺改造包括电炉炼钢和氢能炼钢,氢能炼钢是利用氢气替代一氧化碳做还原剂炼钢,还原过程中没有二氧化碳的排放,可实现钢铁生产完全脱碳,是未来发展方向。
政策青睐
工业脱碳引关注
原材料工业包括石化化工、钢铁、有色金属、建材等行业,是实体经济的根基,是支撑国民经济发展的基础性产业,也是工业绿色发展的主战场。“十四五”期间,面对资源能源和生态环境的强约束、碳达峰碳中和的硬任务,原材料工业绿色和安全发展的任务更加紧迫。
中国科学院院士、中国产业发展促进会氢能分会专家委员会主任徐春明指出,在双碳背景下,这些关系国计民生、支撑实体经济发展的行业亟须完成转型升级,提质增效的同时脱碳压力较大。他强调,“尽管目前工业产氢用氢成本相对较高,但其‘零碳’属性目前还没有其他大宗原料可以替代,而且它可以完全由可再生能源生产,因此氢在这些领域的脱碳中可以发挥关键作用。”
对此,蒂森克虏伯(中国)投资有限公司技术研发和可持续发展负责人田昊也认为,工业自身的排放以及工业所需能源的排放占比很高。其中,钢铁、水泥、化工等制造业都是传统高排放的行业;而从治理的角度,工业排放则最为集中,减排效率和影响更为突出。他同时表示,从工业脱碳的角度,无论是钢铁行业,还是水泥或化工行业,未来都需要使用大量的绿氢替代化石能源和原料,“利用氢能推动工业领域减排,将成为大势所趋”。
在钢铁冶金行业,氢能发挥的作用尤为明显。“钢铁行业一直有两个‘帽子’,高污染和高能耗。”内蒙古赛思普科技有限公司副总经理周海川告诉记者,传统的碳冶金会产生大量二氧化碳排放,而采用氢作为钢铁冶炼过程中的还原剂,不仅可以减少碳排放,提高还原效率,还为冶金全流程生产过程产生的富氢含碳煤气找到了更有价值的利用途径。
《规划》中要求,“到2025年,钢铁、有色金属、建材等重点行业能源消耗总量、碳排放总量控制取得阶段性成果”,而氢能成为技术和项目布局的重点方向。在徐春明看来,国家政策的扶持和鼓励,有利于形成我国在该领域的原始创新成果,加快资本、技术和人才等要素向氢能产学研用聚集,促进在具备技术经济可行性的领域先行先试,快速落地,产生示范效应。
积极转型
冶金化工谋变革
作为全球“排放大户”,工业领域中的冶金和化工行业正积极以氢能促变革,减少二氧化碳排放。其中,德国蒂森克虏伯钢铁集团是全球首家在炼钢工艺中使用氢气代替煤炭以减少碳排放的钢铁集团。早在2019年11月11日,该公司就已启动氢能冶金的测试,将氢气注入杜伊斯堡9号高炉,这是全球范围内钢铁公司第一次在炼钢工艺中使用氢气代替煤炭。
根据蒂森克虏伯的气候战略,该公司至2030年碳排放将减少30%。田昊介绍,蒂森克虏伯在工业领域有着丰富的业务,在钢铁、水泥、化工等方面都面临减排的压力和机遇。他表示,“我们作为一个工业企业,面对欧洲绿色发展和碳税的预期,减排势在必行,与其等碳税来革我们的命,不如我们主动迎接这一机遇。”
而在国内的工业领域,氢在化工、炼钢、建筑等应用场景已有较多尝试。徐春明告诉记者,当前,化工行业产能过剩趋势放缓,正在向绿色化、高端化方向发展,包括合成氨和炼化在内,化工细分行业的氢消耗量正在快速攀升。与此同时,我国冶金行业正在积极转型,开展富氢碳循环高炉工艺、氢基竖炉直接还原和尾气CO2捕集及资源化利用等方面的技术推广和示范。
据业内统计,目前,国内已有宝武、河钢等8家龙头企业开始布局氢冶金。其中,北京建龙重工集团的控股子公司——内蒙古赛思普科技有限公司已于2021年4月,实现年产30万吨氢基熔融还原高纯铸造生铁项目成功出铁,标志着氢基熔融还原冶炼技术成功落地转化。周海川表示,早在2016年,建龙集团就提出绿色低碳冶金技术的研发布局,并联合北科大、东北大学、辽科大、唐钢国际和中钢热能院等科研院所成立“氢冶金实验室”,经过两年多的研究,开发出氢基熔融还原的新工艺。
周海川还介绍,今年,按照建龙集团的规划,赛思普将建成第二代采用纯氢冶炼的中试装置,从“富氢”阶段迈向“全氢”阶段。未来,该公司还将在2025年实现等离子化全氢冶炼,并联合国内制氢权威机构研究生物质和生活垃圾制氢,利用生活垃圾富余的碳水化合物制氢,在获取钢铁冶金所需还原剂的同时,助力解决城市生态问题。
宏图起笔
创新突破是关键
从中长期来看,我国可再生能源资源丰富,在绿氢的供给上具有巨大潜力,将有助于实现化工、冶金等工业难以减排领域的深度脱碳。中国产业发展促进会氢能分会预计,随着技术成熟和清洁氢的应用,我国钢铁行业2025年前后可实现工艺成熟,对氢需求达36万吨/年,有望实现行业碳达峰。
为实现这一目标,可再生能源制氢的规模化和技术创新十分重要。田昊表示,可再生能源电解制成的绿氢将大规模应用到高排放工业领域,到2030年,将有500万吨氢来自于80GW的电解装置。他强调,制氢的技术未来会呈现出多元且迭代迅速的状况,而推动其发展很重要的一点在于规模化,必须要有产业来拉动。
对此,周海川认为,从制氢的角度,未来要控制好灰氢、蓝氢、绿氢的结构比例。“要让绿氢占比更多,碳中和才有‘落脚点’。”他还指出,在应用环节,需要从政策上使氢基冶炼拥有“绿色标识”,并通过碳税等方式调节成本,倒逼企业转型,引导市场消费,多用绿色技术生产的产品。
徐春明告诉记者,在全球通货膨胀、产能过剩的大背景下,钢铁、化工和冶金行业正在实施节能减排、技术改造和优化升级等工作,这些行业积极结合双碳需求开展用氢示范,研发、设计和配套装备制造等行业热情较高,管理部门也正在大力鼓励,降低土地等生成要素的成本,加大税收和补贴等方面的支持。
业内普遍认为,通过氢能发展推动工业减排的宏图已经起笔,而氢能制、储、输、用各环节的技术突破是关键。国家发展改革委价格成本调查中心强调,为实现双碳目标,钢铁行业要积极探索降本增效应对之策。钢铁生产需为工艺改造付出更多成本。短期来看技术研发、工艺改造需要不断的成本投入,长期而言将降低碳排放,减少碳排放成本。