相比于陆上风电,海上风电所处环境更为复杂,海洋大气区高湿度、高盐雾、长日照,浪花飞溅区干湿交替,水下区海水浸泡、生物附着等,腐蚀环境非常苛刻,这给海上风电设备的腐蚀防护带来了严峻挑战。海洋腐蚀不仅会缩短机组运营寿命,给海上风电机组带来巨大安全隐患,而且也会大大增加海上风电的建设投资和运行维护成本。因此,防腐蚀是海上风电必须考虑的问题,防腐蚀设计也因此成为海上风电场设计的重要环节之一。前期文章“防腐技术在海上风电场中的应用”主要对腐蚀环境、防腐方法和技术应用等方面进行分析,本文重点介绍海上风电设备腐蚀机理及检测方法。
海上风电设备腐蚀现状
无论是海上风电还是其他海洋工程,海洋腐蚀以及生物污损都严重威胁着这些重大工程设施的安全运行。然而,目前大多数海洋工程结构处于裸露或欠保护状态,海洋工程结构安全堪忧,腐蚀损失巨大。如何保证各种海洋工程设施的耐久性和安全性,降低重大灾害性事故发生,延长这些重大工程设施的使用寿命,是当前我国海洋经济发展中需要迫切解决的关键性问题和共性问题。目前,我国海上风电防腐蚀方面主要存在以下问题:
我国海上风机腐蚀防护技术还不完善,缺少一套海上风电整体防腐的体系标准。
防腐设计基础相对薄弱,相关人员对海上风电设备防腐认知不足。所有产品的防腐设计都应当依据产品自身服役环境的特点来制定对应的产品防腐方案。海上风电设备防腐设计的重点在于其防腐环境特别恶劣,防腐技术要求高,且难以进行二次维护。因而,在对海上风电设备进行防腐设计时,必须对其服役环境进行具体了解,并且掌握所使用材料的各种物化性能(耐老化性、耐盐雾性、导电性等),掌握一些基本的产品防腐结构设计方面的知识,才能够进行合理而可靠的产品防腐设计。
海上风电防腐蚀是一个系统工程,从涂层体系配套、涂料选用、表面处理、涂装施工到安装运行阶段,都需要进行严格控制。现阶段,国内海上风电配套体系方案少,国内设备供应商对海上风电设备涂装工艺的积累不足,安装、运营单位对设备的维护和保养的经验欠缺等,这些因素都会影响到海上风电设备的防腐性能。
海上风电设备腐蚀机理
海洋环境是腐蚀性最为严酷的自然环境。海水是一种具有很强腐蚀性的电解质溶液,含有大量盐类, 包括氯化钠及含有钾、溴、碘等元素的盐类。海水中溶解有氧气、氮气、二氧化碳等气体,而其中的氧气是引起海水中碳钢、低合金钢等金属结构物腐蚀的重要影响因素。表层海水氧气是饱和的,约为8mg/L,腐蚀性更强。海水温度呈周期性变化,一般来说,钢铁等的腐蚀速度会随着海水温度的升高而增加。另外,海水中含有丰富的氧微量元素和营养盐类等,这为海洋生物的生存和繁殖提供了必要条件。而海洋生物的存在则会影响金属材料的腐蚀行为与机制。
海水与空气接触面积大、对流充分,在海浪的不断搅拌下,氧气饱和、湿度极大,加快了海上风电设备的腐蚀速率。风电机组“有风发电、无风停机、超风速急停”的不均匀运转模式会产生高频交变应力的疲劳荷载作用,这导致了风电机组腐蚀疲劳加速,严重影响了海上风电机组的使用寿命。
海上风电场的防腐措施尽管可以在很大程度上参考海洋平台现有的防腐经验,但是二者之间也有较大不同。海上风电场是无人居住的,并且严格限制人员的接近。海洋平台是有人居住的,海洋平台上的防腐涂层检查和维修可更容易且有计划地进行,受到腐蚀时可以随时修补。而海上风电场很难做到这一点,维修费用极高,后续维护费用是其成本的7倍以上。因此,应当更加重视海上风电机组的钢结构腐蚀,特别是外露于海洋大气和飞溅区中的部位。一般情况下,大气区结构件采取涂料保护或热喷涂金属保护,如大气区钢结构一般采用环氧富锌底漆(含锌≥80%)、环氧云铁漆、聚氨酯面漆(或者聚氨酯+氟碳双重面漆)3层涂层体系;飞溅区钢结构一般采用玻璃鳞片漆、环氧耐磨漆双层涂层体系;全浸区一般采用玻璃鳞片漆、环氧厚浆漆双层涂层体系,并采取牺牲阳极进行协同防腐。
此外,目前风电行业往往主要关注海上风电结构件腐蚀,对电器设备腐蚀问题缺乏系统性认识和解决方案,一般来说,海上风电机组的关键电器设备更易受盐雾的侵蚀,电器设备故障率会明显上升。考虑到海上风电电器设备的种类繁多,重点应从改善电器设备服役环境条件着手,主要措施包括:在提高机舱及塔筒密封性的同时,应增加空气净化防腐系统,去除塔筒、机舱或者集装箱内部的盐雾,并且降低空气的湿度。依据塔筒、机舱或者集装箱内部实际空间的大小,可以确定所需的空气净化防腐系统净化风量;此外,盐雾净化处理应去除 90%以上海洋环境中独有的腐蚀性盐分颗粒。
腐蚀检测方法
为了更好地分析海上风电设备的腐蚀情况,以某海上风电场的风机及升压站的评估结果为例,从涂层使用状态和完整性、阴极保护及牺牲阳极使用状态检测、可溶性盐分含量检测等方面,探讨海上风机、升压站的腐蚀检测分析方法。
1、涂层使用状态和完整性
通常采用的检查方法一般为在自然光照射下,检查人员目视检查涂层变色、粉化、开裂、起泡、长霉、生锈和剥落等缺陷,对涂层表面目视可见的均匀破坏采用破坏的变化程度进行评级,非连续性或其局部不规则破坏采用破坏数量进行评级,具体评级参照《GB/T 30789 色漆和清漆涂层老化的评价》。此外,依据能源部标准《NB/T 31006-2011 海上风电场钢结构防腐蚀技术标准》要求,对钢管桩干膜厚度进行测量,评价标准为:所有测点干膜厚度的平均值应不低于设计干膜厚度,所有测点的干膜厚度应不低于设计干膜厚度的80%,80%以上测点的干膜厚度应达到设计干膜厚度的要求。
以往海上风电风机设备腐蚀测量多是在钢管桩、塔筒外壁、塔筒内壁各选择若干测区进行测量,每个测区采用五点取样法进行测试,最终计算所有测试结果的算术平均值作为该测区的平均干膜厚度。
通过对过往风机和海上升压站在海洋大气区、海水飞溅区、潮差区的腐蚀状态进行检查时可以发现,风机和海上升压站钢管桩水上部分防腐涂层表面状况大部分良好,未发现明显的变色、粉化、裂纹、起泡现象,部分风机钢管桩局部有小面积破损、脱落和锈蚀情况;风机附属结构(爬梯、平台、船靠等)局部腐蚀比较严重,很多腐蚀都是由于初期建设阶段涂层损坏未及时修复引发的,且多数钢管桩潮差区被海生物覆盖。具体见图1。
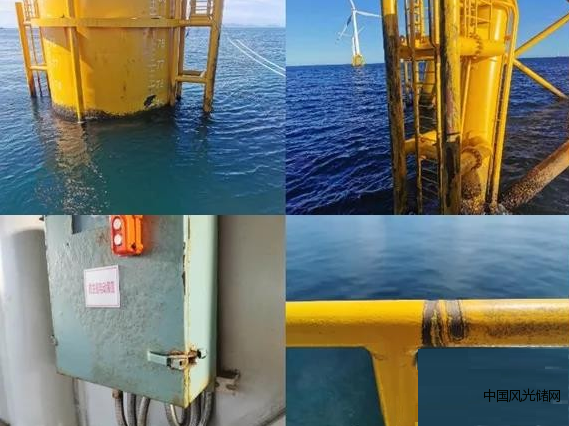
图1 风机钢管桩及附属结构局部腐蚀及海生物附着图片
涂层厚度方面,多是根据风电场提供的风机基础设计信息,检测的位置多为导管架钢桩表面涂层、塔筒内壁涂层、塔筒外壁涂层等。一般而言,若基础钢管桩涂层干膜厚度小于原设计厚度,且低于原设计厚度的80%,便已不符合标准要求,说明风机基础钢管桩涂层厚度较差。不过,还需结合现场的检测情况做最终判断。很多时候比设计值偏小的涂层多为修复过后的的涂层,主要原因应该是吊装施工过程中涂层损坏之后的修复没有严格按照涂层设计要求进行。
此外,若塔筒内壁不存在损坏修补过程,而且使用时间也比较短,测量干膜厚度基于等于出场干膜厚度。这说明,塔筒内壁的厚度并没有经过严格检测,未在确保合格后即出厂。表1为某风机设备抽取的的部分测量数据实例。
表1 风机升压站涂层厚度测量结果
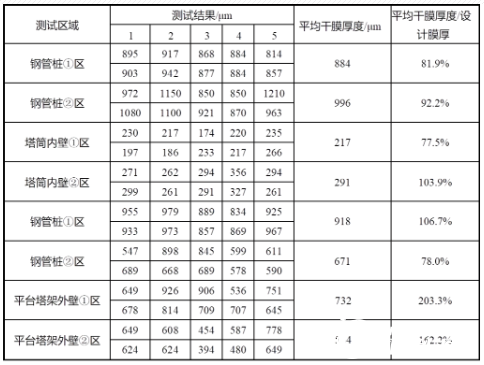
2、阴极保护及牺牲阳极使用状态检测
电位检测也同样很重要,一般采用铜/饱和硫酸铜参比电极、高阻抗数字万用表,自水面向下取平均水深约5m范围内进行检测。检测共选取若干方位,逆时针排序检测,每隔约120°为一个检测方位,每个检测方位以电极接触水面开始检测,向下放电极每间隔约1m记录一个测量值,检测示意图见图2。
按照规范规定,采用牺牲阳极保护时,钢质港工设施最小保护电位应达到-0.85V(相对铜/饱和硫酸铜参比电极,以下同),最大保护电位不超过-1.10V。
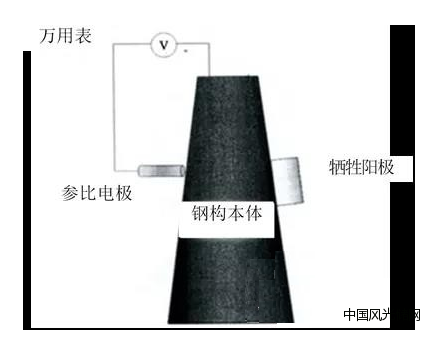
图2 阴极保护电位检测示意图
牺牲阳极使用状态检测由专业潜水检测人员携带摄像设备、清理工具、测量工具,潜水员用钢丝刷、斧头或其他工具清除阳极和焊缝表面的腐蚀产物及其他附着物,露出阳极和焊接部位的本体表面。
牺牲阳极使用状态检查时,需要对每台风机随机抽取的牺牲阳极进行探摸检查和测量尺寸。过往检查就曾发现,多数牺牲阳极表面均会被海生物覆盖,需用工具才可清除,牺牲阳极表面溶解较好。阳极焊脚焊接情况良好。如果设备使用时间较短,那么阳极块整体的损耗一般不大,大部分的测量数据基本都会在设计值或之上,不太会出现损耗较大的牺牲阳极块,剩余使用寿命基本与设计使用寿命一致。
此外,对清理干净的牺牲阳极本体和铁脚部位还需要求进行录像检测,并随机抽取每台风机的若干个牺牲阳极用软尺对阳极上、中、下不同位置的周长及阳极长度进行测定。船上检测人员进行实时监测和录像操作,并测量阳极表面局部蚀坑的深度。船上检测人员记录阳极表面状况,记录检测数值。
3、可溶性盐分含量检测
通常根据《GB/T 18570.6-2011 涂覆涂料前钢材表面处理 表面清洁度的评定试验 第6部分:可溶性杂质的取样Bresle法》,目前多是采用Bresel法测试现场各塔筒内表面含盐量,并随机抽取一定数量风机测试机舱内表面、升压站开关室和塔筒外壁进行含盐量检测,其原理为测量所有水溶性盐离子的电导率,并将其换算成单位面积上的NaCl含量。目前国内、国际对涂层表面的可溶性盐分无统一的数值标准,业界公认的可溶性盐分的允许值为100mg/m2, 某不同浓度可溶性盐分对涂层的影响见表2。
表2 可溶性盐分含量对涂层的影响
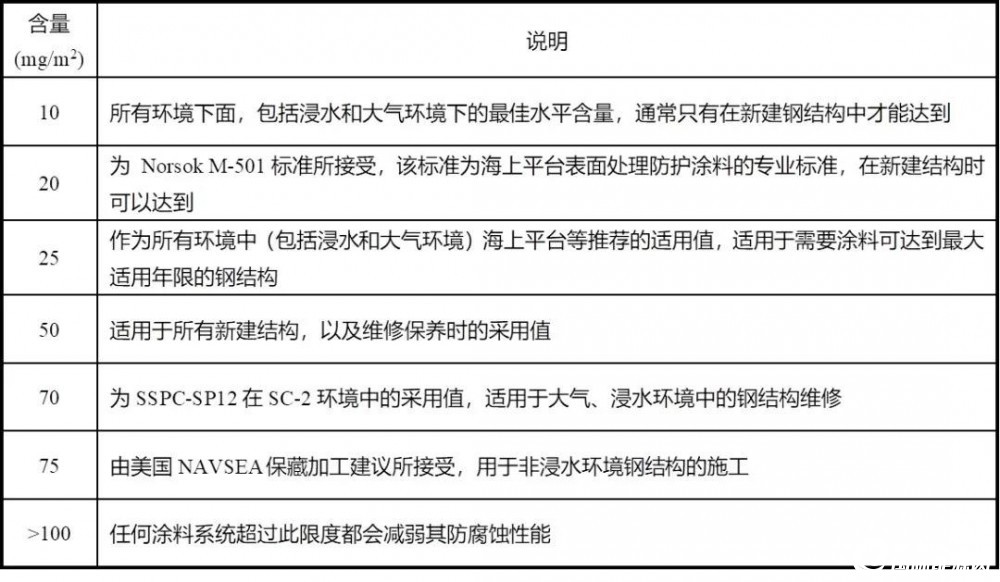
通过以往检测结果可以发现一些规律,升压站从一层逐渐往上含盐量是有明显降低的趋势,风机从塔筒底部内壁至机舱也有该趋势,可能是因为升压站一层及风机塔筒底部人员活动频繁,相应的设备间、塔筒门的开关频繁,与海洋大气接触较多,表面盐分沉积增多。塔筒外壁虽然一直处于海洋大气环境中,测试结果低于绝大部分的室内测试数据。
结语
随着我国海上风电开发和利用的速度加快,迫切需要结合我国的实际情况深入开展海上风电机组的腐蚀防护等关键性技术研究,同时加快海上风电机组腐蚀与防护技术的应用探索,从而助力海上风电产业的健康发展。